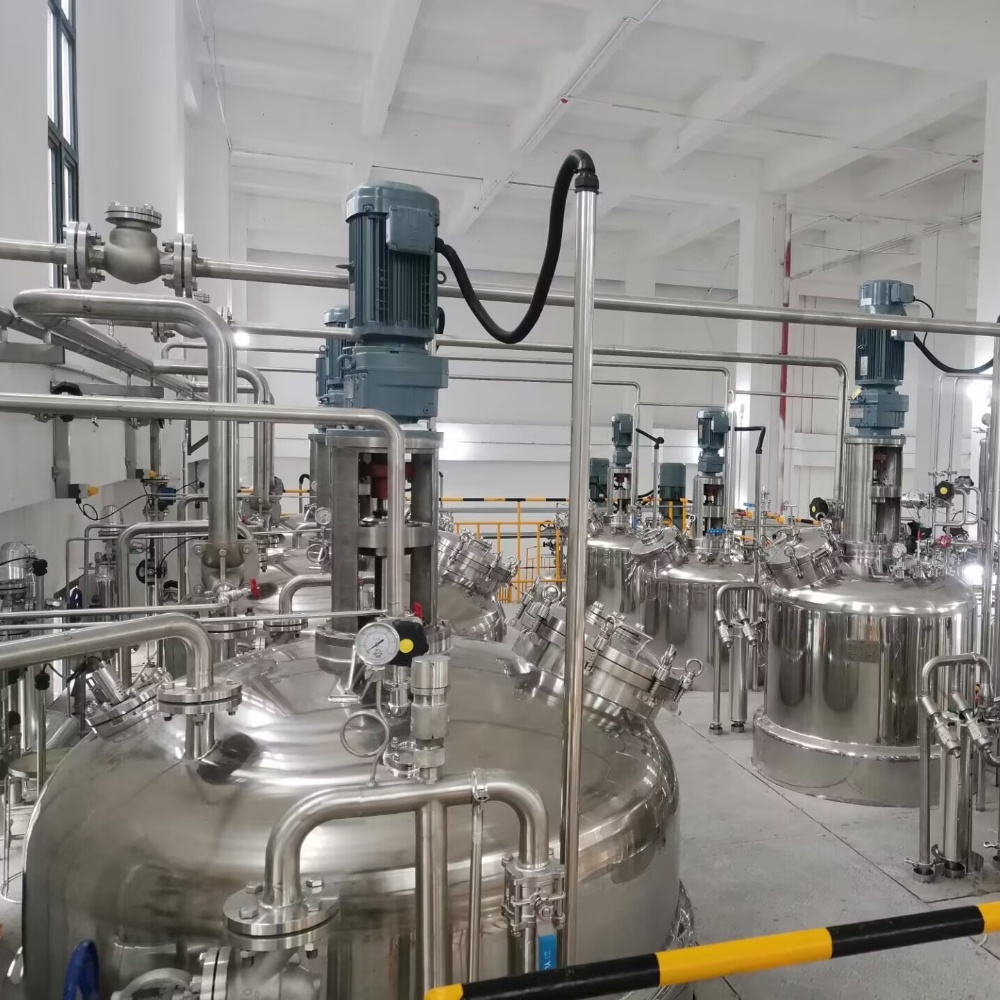
The full volume of commonly used fermentation tanks in laboratories is usually between 2 liters and 500 liters, 500 liters to 5000 liters are pilot fermenters, and the full volume of fermenters used in actual industrial applications is usually above 5000 liters. Industrial fermenter can withstand steam sterilization, have certain operational flexibility, minimize internal accessories (avoid dead corners), have strong material and energy transfer performance, and can be adjusted to facilitate cleaning and reduce pollution. They are suitable for the production of a variety of products and reduce energy consumption.
Bailun 10KL industrial fermenter
1.Characteristics of industrial fermenter
The basic structure of the industrial fermenter usually consists of several components, including the tank body, heating system, cooling system, pressure control system, sensor and control system, stirring system, and inlet and outlet. The specific structure and configuration of the industrial fermenter will be designed in combination with the usage scenario. Some industrial fermenters may also be equipped with additional equipment, such as dissolved oxygen control systems, pH sensors, etc., to provide better control and monitoring.
The biggest difference between industrial fermentation and other chemical industries is that it is a chemical reaction carried out by organisms. Its main characteristics are as follows:
1.The fermentation process is generally a biochemical reaction carried out at normal temperature and pressure, which is safe and requires relatively simple conditions.
2.The raw materials used for fermentation are usually starch, molasses or other agricultural and sideline products, and the reaction can be carried out by adding a small amount of organic and inorganic nitrogen sources. Microorganisms can selectively use the nutrients they need due to different categories. Based on this characteristic, wastewater and waste can be used as raw materials for fermentation to transform and update biological resources.
3.The fermentation process is completed by the automatic adjustment of organisms, and the reaction is highly specific, so a relatively single metabolite can be obtained.
4.Due to the reaction mechanism of the organism itself, it can specifically and highly selectively carry out chemical transformation reactions such as oxidation and reduction of certain complex compounds, and can also produce relatively complex polymer compounds.
5.The prevention and control of bacterial contamination during the fermentation process is crucial. In addition to strict disinfection of the equipment and air filtration, the reaction must be carried out under sterile conditions. If contaminated with bacteria, production will suffer huge economic losses. If infected with bacteriophages, fermentation will cause greater harm. Therefore, maintaining sterile conditions is the key to the success of fermentation.
6.Microbial strains are the fundamental factors for fermentation. Through mutation and strain screening, high-yield excellent strains can be obtained and production equipment can be fully utilized, and products that are difficult to produce by conventional methods can also be obtained.
7.Compared with other industries, industrial fermentation has less investment, quick results, and can achieve significant economic benefits.
Based on the above characteristics, industrial fermentation has attracted more and more attention. Compared with traditional fermentation technology, modern fermentation engineering has more advantages besides the above fermentation characteristics. In addition to using microorganisms, animal and plant cells and enzymes can also be used, and artificially constructed “engineered bacteria” can also be used for reactions; the reaction equipment is not just conventional fermentation tanks, but is replaced by various bioreactors, with a high degree of automation and continuity, which improves and innovates the fermentation level on the original basis.
Bailun 60T-10T industrial fermenter
2.Components of the fermentation process:
(1)Setting the components of the culture medium used for breeding seeds and fermentation production;
(2)Sterilization of the culture medium, fermentation tank and its ancillary equipment;
(3) Cultivating active and appropriate pure strains and inoculating them into the production container;
(4)Microorganisms grow in the fermentation tank under the conditions most suitable for product growth;
(5)Product extraction and refining;
(6)Treatment of waste discharged during the process.
Schematic diagram of the fermentation process
The operation of the industrial fermenter must first be technically prepared, that is, check whether the power supply, pipelines, air compressor, and circulating water system are normal. Then, air disinfection is carried out before feeding to ensure that the system is in a sterile state.
After the industrial fermenter is dehumidified, add culture medium for actual disinfection. After sterilization, the industrial fermenter is cooled to a suitable temperature and the required bacteria are introduced for fermentation operation.During the fermentation process, sampling and testing are carried out in accordance with standardized aseptic operations. After fermentation, discharge the materials and clean the industrial fermenter.
Industrial fermenters are also prone to contamination and scaling, especially when the culture medium is actually eliminated in the tank. Therefore, we should establish the concept of “prevention first” and start from the equipment to eliminate various hidden dangers that may cause industrial fermenters to be contaminated.
(1) Ensure the tightness of industrial fermenters
Industrial fermenters are the main equipment for industrial fermentation production. Before use, the industrial fermenters needs to be carefully inspected, such as whether its stirring system rotates abnormally, whether the mechanical seal is tight, whether the screws in the tank are loose, whether the pipes in the tank are blocked, whether the interlayer or the coil in the tank is leaking, and whether the tank body connection valve is tight.
At present, mechanical seals are widely used in industrial fermenters, which replace the previous packing seal form of the stirring shaft. However, if the installation accuracy is not high or the selected mechanical seal system is not suitable, the shaft seal will still leak and cause bacterial contamination. Therefore, pay attention to alignment when installing the stirring shaft.
(2) Remove the sight glass flushing pipeline of the industrial fermenter
In order to facilitate the observation of the fermentation situation in the industrial fermenter, a steam pipe for flushing the sight glass is generally set in the industrial fermenter. However, once the steam condenses in the pipe, it cannot completely guarantee the sterility of the condensed water. Therefore, the steam pipe for flushing the sight glass should be removed to reduce the risk of bacterial contamination. If it is difficult to see clearly due to the heavy fog in the tank, a higher brightness sight glass lamp can be used.
(3)Industrial fermenter use PVDF membranes
The traditional air purification system uses activated carbon, cotton, and ultra-fine glass fiber paper as filter elements, which have poor filtering effects and are complicated to operate. At present, domestic membrane filtration technology has become relatively mature. For example, the folded microporous membrane filter element made of polyvinylidene fluoride (PVDF) not only has high filtering accuracy but also has a large flow rate.
When using industrial fermenter, technicians only need to pay attention to dehumidifying and deoiling the compressed air before the filter and sterilize the filter according to the specifications to ensure that the air is sterile. In addition, since the PVDF membrane is not sensitive to moisture in the compressed air and the membrane itself has strong hydrophobicity, it can solve the problem that cotton filters cannot be used when the air humidity is too high.
(4) Regularly inspect the monitoring system of industrial fermenter
The thorough sterilization of the fermentation medium is to use high-temperature supersaturated steam to coagulate and kill various bacteria and fungal proteins. In the sterilization of the pharmaceutical industry, there are strict requirements for preheating time, steam valve opening, sterilization temperature, sterilization pressure and foam control. Any problem in any link can easily lead to bacterial contamination.
Generally, the sterilization temperature in industry is 110℃ and the sterilization pressure is above 0.5 MPa. The accuracy of sterilization temperature and pressure depends on monitoring systems such as various temperature probes and pressure sensors. Therefore, it is very important to regularly test such probes and sensors. In addition, as the volume of industrial fermenter increases, the tank temperature corresponding to the same tank pressure decreases. Therefore, when the correlation between temperature and pressure changes, the temperature should be used as the standard.
(5) Soft seals are used for industrial fermenter valves
Industrial fermenter valves are the most commonly used auxiliary equipment in fermentation equipment, among which the most commonly used is the stop valve. The sealing performance of valves to the medium can be divided into four levels, namely nominal level, low leakage level, steam level and atomic level. Nominal level and low leakage level seals are suitable for valves with loose closing requirements, such as valves used to control flow.
Steam level seals are suitable for the sealing of valve seats, valve stems and valve body connections of steam and most other industrial valves. Atomic level seals are suitable for occasions with extremely high requirements for medium sealing, such as spacecraft and atomic power equipment. Since high-temperature steam is used to sterilize fermentation equipment in the fermentation industry, the sealing performance of valves to the medium requires steam level seals.
Soft-sealed valve closing parts generally use soft gaskets, which use the large elastic-plastic deformation of the gasket to form a wider annular sealing contact zone to fill the unevenness on the sealing surface and eliminate the gap to form a seal. The processing accuracy is generally not high.
If there are special requirements, the valve body material can be made of stainless steel, and the soft sealing closing part can be replaced with a replaceable polytetrafluoroethylene gasket. In this way, the sealing of the valve can be ensured by frequently replacing the polytetrafluoroethylene gasket.
(6) Checking the upper seal of industrial fermenter valves
If the processing quality of the valve stem and the inner hole of the valve body of the industrial fermenter stop valve is not good, or the matching clearance between the packing and the valve stem increases due to wear caused by long-term use, the medium will leak from the valve stem. This phenomenon is called “upper seal leakage” of the valve. However, in industrial fermentation production, the upper seal inspection of the valve is often neglected. Therefore, for valves used for fermentation, it is necessary to pay attention not only to the leakage of the sealing substructure, but also to the upper seal leakage.
In industrial fermentation production, due to the requirements of the fermentation process, some valves are not installed according to the flow direction of the fluid. For example, in some industrial fermenters, the sampling valve is a DIY valve close to the industrial fermenter. In order to sterilize the valve before sampling, the valve is installed in the opposite direction of the fermentation liquid flow, so that a small additional valve can be installed at the bottom of the sampling valve to allow steam to flow.
The upper sealing structure of the sampling valve has very high sealing requirements, otherwise the fermentation liquid may penetrate into the upper sealing structure of the sampling valve or even leak from the upper sealing structure, causing the industrial fermenter to be contaminated.
At present, most domestic stop valves have a multi-layer packing structure, and a hard spacer ring is also added to the packing structure, or a disc spring is provided on the upper part of the sealing ring, thereby improving the ability of the sealing force to self-regulate and improving the sealing performance. If the upper seal leaks, and it is difficult to change the upper sealing structure of the domestic valve, the leakage problem can be solved by changing the type of packing.
Prevention of bacterial contamination in industrial fermenters:
- Perform sterile operation in industrial fermenter
- Seeds must not have foreign bacteria
- Air filters must be kept in good quality
- Be careful not to have too much foam
- Ensure the sterility of the air system
- The airtightness of industrial fermenters,especially some dead corners, must be paid special attention to
- If you want to transplant seeds, you must also ensure the sterility of the pipelines and dead corners
- Ensure that the seeds are normal, without contamination and variation
- If there is mid-term feeding, the feeding system must be ensured to be sterile
About Bailun
Bailun has rich experience in the manufacture of various bioreactors and pressure vessels. It has a team of experts in the fields of biological reaction, fermentation technology, machinery manufacturing, and automation control. The scientific research and process level is always at the leading domestic and international first-class level, providing you with a comfortable, assured, and secure product experience.
Contact Us:
Add:6848# Liuxiang Rd., Jiading, Shanghai, China
Contact Person: Maddie
Email:sales@fermentertech.com
Phone:+86-134-7276-8163 (WhatsApp)
Website: https://bioreactortech.com/