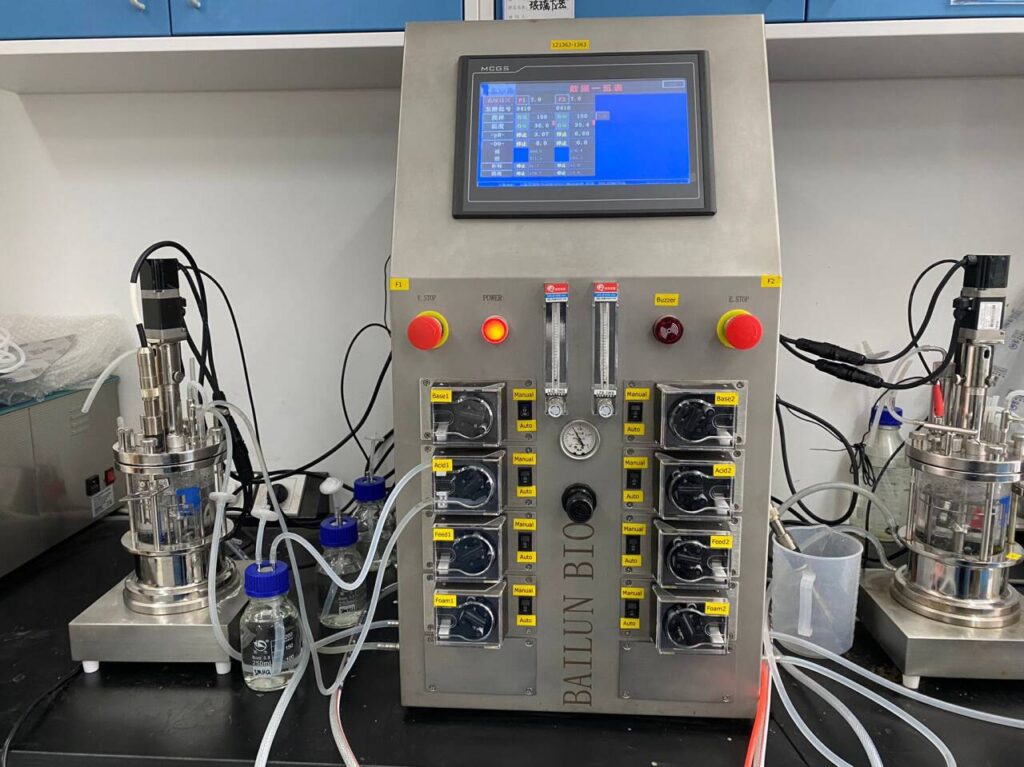
Characteristics of laboratory bioreactor
As a highly specialized experimental equipment, the characteristics of laboratory bioreactors are mainly reflected in the following aspects:
- . Precise environmental control: The bioreactoris equipped with a sophisticated control system, which can accurately monitor and adjust the temperature, pH value, dissolved oxygen and other key parameters in the tank, providing a stable and controllable environment for the growth and fermentation of microorganisms. This accurate environmental control is important for the growth characteristics and metabolic pathway of microorganisms, which can ensure the reliability and repetitiveness of the experimental results.
- Excellent material: The tank body is usually made of high-quality stainless steel or glass material, which not only has good corrosion resistance and sealing, but also can effectively resist the corrosive substances that may be produced during the fermentation process to ensure the smooth progress of the fermentation process. In addition, the easy cleaning of the material also ensures the long-term stable operation of the equipment and the accuracy of the experimental results.
- High degree of automation: Modern laboratory bioreactors generally have automatic control functions, which can realize fully automated production, simplify the production process and improve production efficiency. Through computer or PLC control, the reaction conditions can be accurately controlled, and the data can be quickly collected, processed and analyzed through visual processing software, which greatly improves the convenience and scientificity of the experiment.
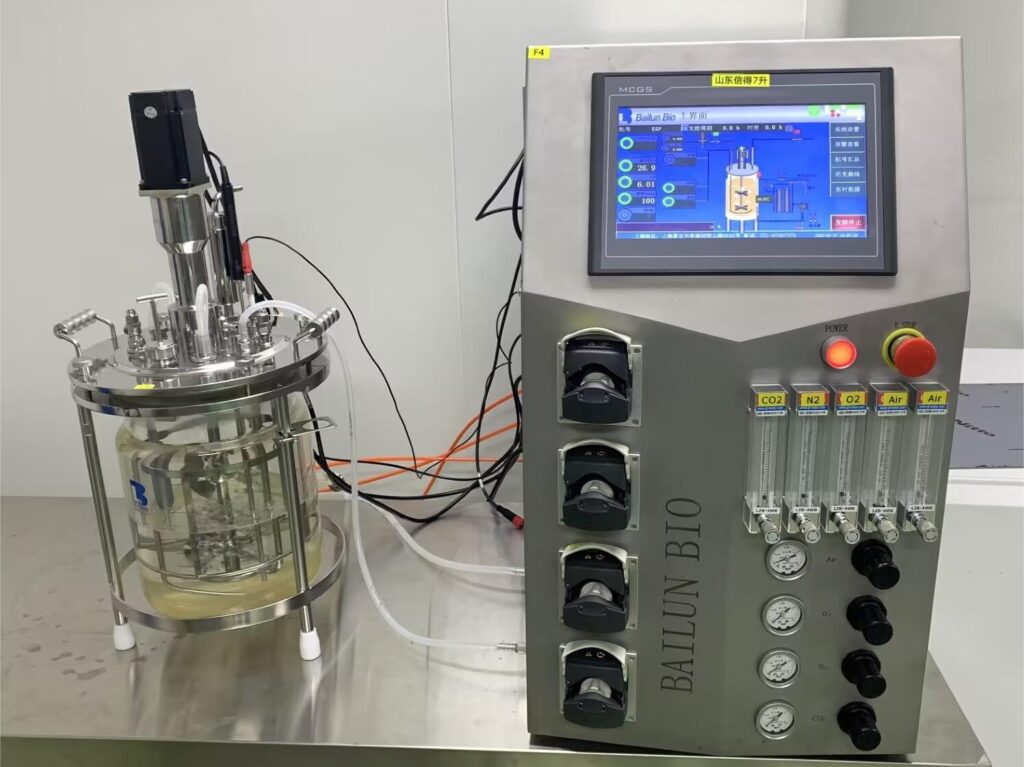
Laboratory bioreactors are indispensable equipment in fields such as bioengineering, pharmaceuticals, and food science for small-scale cultivation of microorganisms and cells. Correct installation and debugging can not only ensure its performance, but also extend the service life of the equipment. There are some practical tips for installing and commissioning your bioreactor.
(1). It is important to choose the right installation location.The laboratory bioreactor tank should be installed on a solid and flat workbench, and ensure that there is enough space around it for operation and maintenance. Avoid installing the device in a humid or corrosive gas environment to avoid damage to the device.
(2). During the installation process, special attention should be paid to the connection of pipes and joints. Use hygienic pipes and fittings to ensure that laboratory bioreactors are connected securely and leak-free. Check that all valves, pumps, and sensors are properly installed and ensure that their functions are normal. Special attention is paid to the quality of the seals to ensure that they are intact.
(3). It is also very important to calibrate the level of the fermenter in the laboratory. Use the horizontal instrument to check whether the laboratory bioreactor is in a horizontal state, and adjust the anchor bolts to ensure stability. This helps to reduce vibration and wear and tear, increasing the operational efficiency of the equipment.
(4). In the commissioning stage, the no-load test run is carried out first. Start the bioreactor, observe whether the operation of each motion component is smooth, there are abnormal sounds or vibrations.Check the mixing system and temperature control system to make sure they are working properly. Adjust the stirring speed and temperature settings as needed.
(5). Carry out load test run. Add an appropriate amount of medium and observe the working status of the laboratory bioreactor to ensure that all parameters (e.g., temperature, pH, dissolved oxygen) are within the specified range. Use standard samples for trial production to check whether the quality and output of the product meet the requirements. If there is any deviation, adjust the relevant parameters in time.
(6). Regular maintenance is the key to ensure the long-term stable operation of the laboratory bioreactor. Develop a detailed maintenance plan, regularly inspect and replace worn parts, clean the inside and outside of the laboratory bioreactor, and maintain a good working environment. Pay special attention to inspect seals and joints to ensure they are intact. These tips are not only for dedicated technicians, but also for casual users who need to install and commission their own equipment.
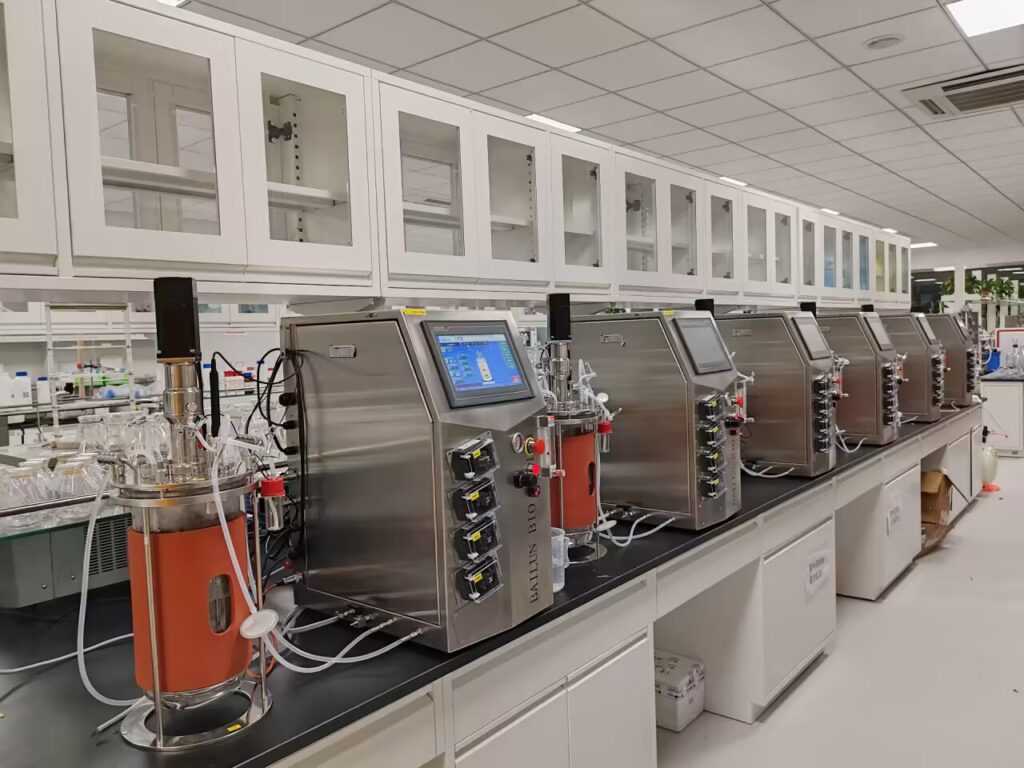
Failure and solution of laboratory bioreactor
In the daily use of laboratory bioreactors, due to operation or damage problems, some fault problems will be encountered, and the following will take you to understand the causes of some common failures and how to solve them.
(1). Failure of temperature control: The fermentation process of the laboratory bioreactor tank needs to be carried out within a certain range, and if the temperature control system is out of control, it may affect the normal progress of fermentation. Failure of the temperature control can be caused by damage to the temperature sensor or leads, or by damage to the temperature gauge.
Solution: Check the sensor and meter, and replace it in time if there is a problem.
(2). After the valve is closed, the pressure is abnormal: gas will be generated during the fermentation of the bioreactor, and if there is a problem with the tank pressure, it will affect the emission of the gas and even lead to an explosion. If the flange fastening screws of the tank cover are not tightened, the sealing ring is damaged, and the pipe joint or valve leaks, etc., the tank pressure will be abnormal and cannot be maintained.
(3). Leakage problem: Strict environmental control is required in the fermentation of bioreactors, and if oxygen enters the tank, it will lead to fermentation imbalance; On the contrary, the leakage of liquid or gas in the tank will also affect the fermentation. Air intake or leakage can be a sealing issue.
Solution: Tighten the fastening screws and the tightness is consistent; Check the sealing ring of the fermentation tank in the laboratory, and replace it in time if it is damaged; Tighten the nut.
(4). Sterilization heating rate is too slow: It may be due to the low steam pressure in the laboratory bioreactor and the insufficient air supply.
Solution: Check whether the electric heating pipe or other heating parts of the fermenter are burned out.
(5). Abnormal pH display: The pH electrode is blocked or damaged.
Solution: Check the pH electrode, clean the electrode, or replace it.
(6). Abnormal DO display: The DO electrode membrane is damaged.
Solution: Replace the DO electrode membrane.
(7). The DO value is too low: the air intake in the laboratory bioreactor is insufficient; clogged filters; The valve of the pipe is leaking.
Solution: If the air intake is insufficient, open a large valve to increase the air supply; Check the filter and replace the filter cartridge if necessary; Check that the valve is tightened.