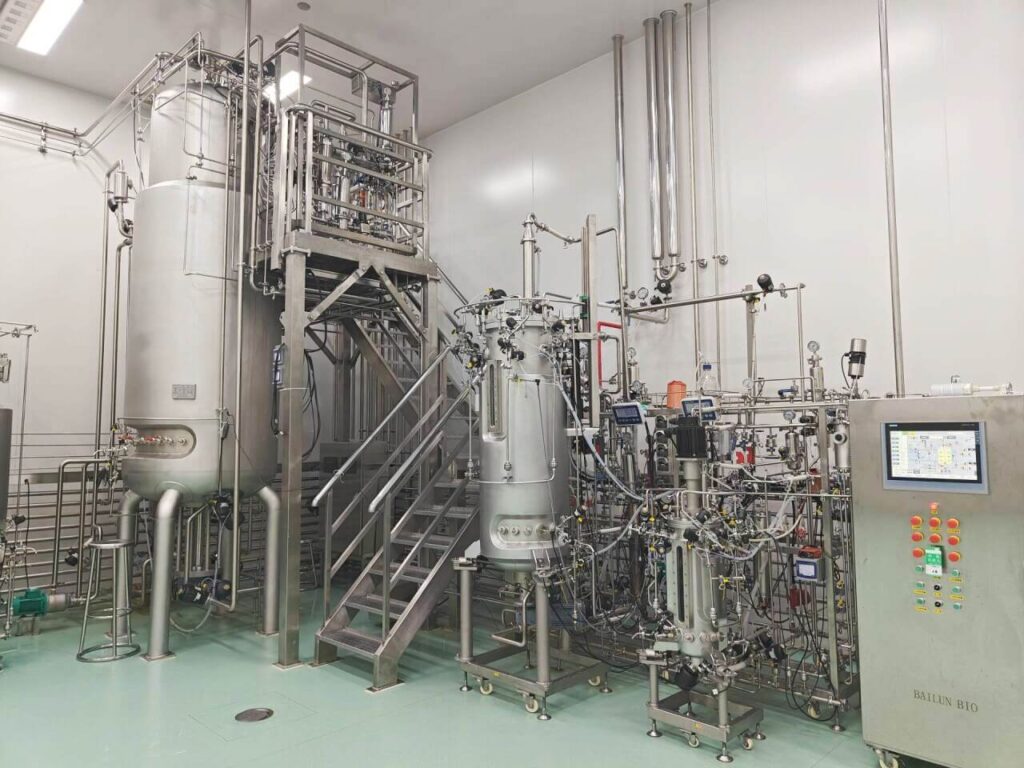
In this blog post, we’ll go deeper into the vaccine production process, going over each step and highlighting the innovations that have shaped modern vaccination production. We will look at one of the most amazing advancements in modern medicine, so stay tuned!
Impact of Vaccines
Before getting into the specifics of the production process, let’s take a moment to think about how vaccines impact our lives. Most of us know of immunization because at one time or another in our lives we have gone through different stages of immunization: infancy, youth, adolescence and maturity.
A complex and sophisticated process is involved in creating these vaccines. Experts have put in years of research, clinical testing, and industrial experience.
Unlike normal infection that makes you have experience of the disease, vaccines help your body to be familiar with the germs which are dangerous to your body. There is always a great danger of a gap between reasonable effectiveness, on the one hand, and reasonable safety, on the other hand.
But more importantly, how and in what ways do we get there? How can a small bacterium or virus be converted into a vaccine that could be spread internationally and protect millions?
The solution lies in the manufacturing of vaccines, a set of correctly orchestrated actions and steps to produce a dose that will be safe, pure, and efficient at the same time.
So, What Is the Process of Vaccine Production?
The process of producing vaccinations is extremely complex and fascinating. It is the result of decades of interdisciplinary collaboration, scientific research, and inventiveness. To completely understand what the vaccine production process consists of, we must first break it down into several crucial components.
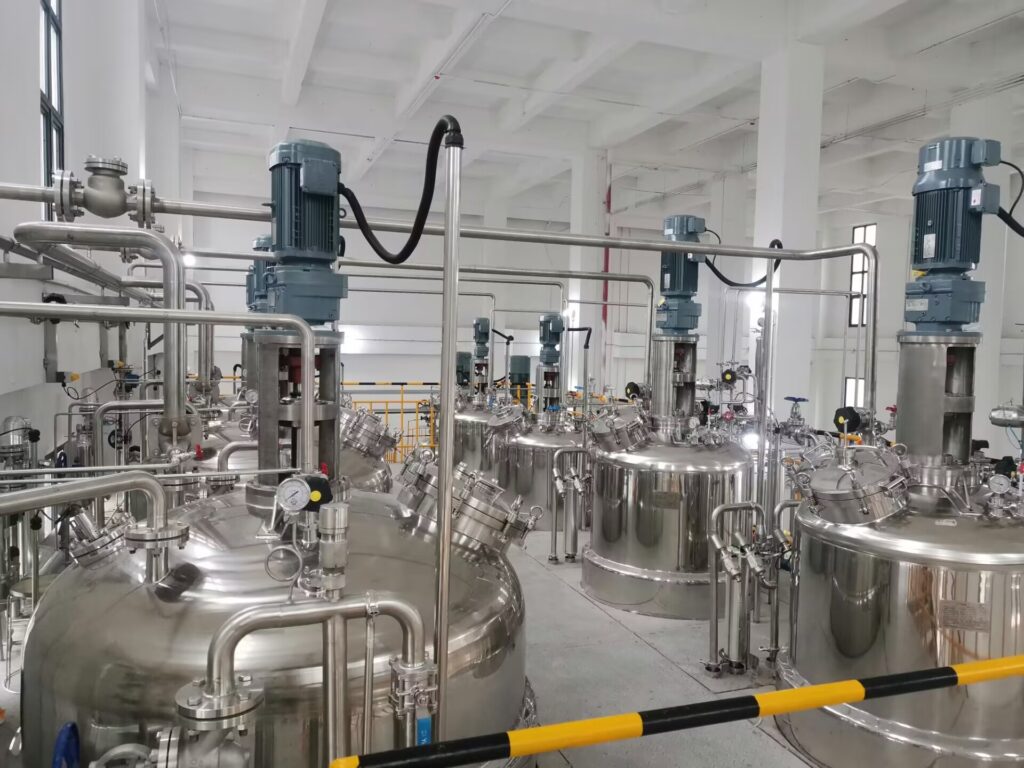
Each of these steps is essential to guaranteeing that vaccinations are both safe and effective.
1. Step One: Research and Discovery: Everything Begins in the Lab
Research is the first stage in the creation of vaccines. Whether a disease is caused by a virus, bacterium, or other microorganism, scientists start by determining which pathogen is to blame. They can determine which portion of the pathogen can be exploited to elicit an immune response once they have a better understanding of how it functions.
This may entail using a weakened or dead strain of the virus itself for some vaccinations, such as the polio vaccine. In other situations, such as the hepatitis B vaccine, researchers might employ just one of the virus’s proteins to boost protection rather than the full virus.
In this early stage, researchers work for years, maybe even decades. To ascertain which antigens are both safe and effective. They examine a variety of them. This is the foundation for the other steps in the vaccine production process.
2. Step Two: Preclinical Research: Assessing Safety at an Early Stage
Following the identification of a potential candidate, preclinical research is conducted, frequently in animals and cell cultures. Before beginning human trials, these investigations help ascertain whether the vaccine elicits an immunological response and guarantees its safety.
Here, scientists assess any adverse effects, calculate the right dosage, and choose the most effective delivery system (oral drops, nasal spray, or injection).

3. Step Three: Tests of the Vaccine in Clinical Trials
The rubber meets the road at this point. Clinical studies are conducted in three stages with human volunteers:
- Phase 1: The safety, dose, and immunological response of the vaccination are evaluated in a small group of volunteers, typically 20–100. Side effects are strictly watched.
- Phase 2: To further evaluate the safety and optimize the dosage and formulation, a larger group (hundreds of people) is tested. During this stage, researchers start to determine whether the vaccine functions as planned.
- Phase 3: To test the vaccine’s effectiveness and further guarantee its safety, thousands to tens of thousands of volunteers are enlisted. This stage collects enough information to assess if the vaccination can stop the illness in practical settings.
Only after completing phases 1 through 3—which can take years—can a vaccine be considered for approval. Additionally, Phase 4 trials are used to assess vaccination safety even after approval in order to guarantee long-term safety.
4. Step Four: Cultivation: Producing the Essential Components
This is when the magic begins to happen! We now have the correct antigen—the portion of the virus that triggers the immune response—after years of investigation and fruitful testing. However, we must produce that antigen on a large scale in order to provide millions of doses.
Regarding Vaccines for Bacteria
- In the event that the vaccine targets a bacterium, such as tetanus, the bacteria are grown in bioreactors, which are sizable fermentation tanks. The industrial fermenters made by Bailun Biotechnology are made explicitly for this purpose. These bioreactors are designed to precisely regulate variables like temperature, pH, and oxygen levels in order to provide the ideal conditions for bacterial growth. After a sufficient number of bacteria have proliferated, they are collected and rendered inactive.
Regarding Viral vaccinations
Human or animal cells are frequently used to generate viral vaccinations. Growing the virus in fertilized chicken eggs is one well-known technique. Newer techniques, however, use sophisticated cell cultures in bioreactors to produce large amounts of the virus.
Cultivating the pathogen or its components to produce enough material to create vaccines is similar to farming.
5. Step Five: Purification and Isolation: Removing What’s Required
The antigen needs to be extracted from the cells or media in which it was generated after it has been created in large enough quantities. Purification is relevant in this situation.
To guarantee that the finished vaccine only includes the active ingredient and no undesirable growth medium byproducts, the purification procedure is essential. Several methods, including chromatography, centrifugation, and filtration, are used to extract the antigens.
Consider vaccinations against microorganisms. Before being refined, tetanus toxoid, the inactivated toxin used in the tetanus vaccine, goes through a formaldehyde detoxification process. This guarantees that the finished product can still elicit an immunological response while being safe.
6. Step Six: Formulation: Mixing the Components
It’s time to incorporate additional components that enhance the vaccine’s effectiveness after the antigen has been purified.
- The purpose of adjuvants is to strengthen the immunological response. To strengthen the body’s immunological response to the antigen, aluminum salts are frequently used in vaccines.
- Stabilizers: Stabilizers guarantee that the vaccine maintains its efficacy throughout transportation and storage. Since vaccines are biological products, improper handling (such as exposure to extreme heat or light) can cause them to deteriorate.
- Preservatives: Preservatives such as thimerosal keep multi-dose vaccines from becoming contaminated. Despite the debate surrounding its usage, thimerosal has been shown to be safe in the small doses included in vaccines.
Together with the antigen, these ingredients make up the finished vaccine, which will be packed and sent all over the world.
7. Step Seven: Packing and Filling: Preparing for Delivery
Vaccines need to be properly packaged before they can be delivered to clinics. This entails putting the vaccine into tiny vials or syringes while maintaining a high level of sterility. A large portion of this labor is done by machines to guarantee accuracy and prevent contamination.
Thousands of vials may be included in a single batch of vaccines, and each one needs to be labeled with details such as the batch number, expiration date, and storage instructions. Quality control is also very important in this situation.
Safety and effectiveness are the top considerations at every step of the vaccine production process, from the preliminary research to packaging. Before being made available to the general public, each batch is tested to make sure it satisfies the requirements.
8. Step 8: The Cold Chain: Maintaining the Effectiveness of Vaccines
Vaccines are delicate items. For many of them to continue working, they must be kept at extremely precise temperatures. In order to maintain vaccines at the proper temperature on their journey from the manufacturing facility to clinics worldwide, a system of refrigerated trucks, storage facilities, and coolers known as the “cold chain” is used.
For instance, many vaccinations must be transported between 2°C and 8°C (36°F and 46°F). They may become less effective after even a brief exposure to higher temperatures.
One of the most important aspects of vaccine production is maintaining this cold chain, particularly in low-resource locations where infrastructure may not be as dependable.
9. Step 9: Post-Production Monitoring: Paying Special Attention
The effort continues even after vaccinations are manufactured, packaged, and delivered. A vaccination is continuously monitored once it is put on the market. Post-marketing surveillance is a procedure that monitors any negative occurrences or side effects that may have gone undetected during clinical trials.
To track vaccine safety in real time, agencies such as the WHO and CDC keep databases. The public and healthcare professionals are also encouraged to report any potential side effects by programs such as the Vaccine Adverse Event Reporting System (VAERS) in the United States. In order to guarantee that vaccines remain safe and effective for everyone, continuous monitoring is essential.
Innovations in Vaccine Production
The manufacture of vaccines has been completely transformed in recent years by advancements in bioreactor technology and biotechnological instruments. Bailun Biotechnology, for example, has led the way in developing scalable, more effective bioreactors that expedite vaccine production. These bioreactors guarantee that safety and quality are always maintained despite generating large amounts of vaccines in shorter amounts of time.
Technologies such as viral vector vaccines and mRNA vaccines have sped up the vaccine development process during the pandemic response. Historically, the development and production of vaccines required years or even decades. However, the ability to produce vaccines more quickly and adaptably thanks to these improved techniques has proven essential in the fight against emerging illnesses like COVID-19.
For example, mRNA vaccines, such as the one created for COVID-19, do not require the pathogen to be cultivated. Rather, they urge the body to manufacture a harmless protein that mimics a portion of the virus using genetic information. Compared to conventional techniques, this invention has shown to be faster and more scalable.
Role of Bioreactors in Vaccine Production
Utilizing bioreactors to cultivate the biological components of a vaccine, such as viruses, bacteria, or certain proteins, is a crucial step in the vaccine production process. Large containers known as bioreactors offer a regulated environment where cells or microorganisms can develop. They also make sure that factors like temperature, pH, oxygen content, and nutrition availability are ideal for the synthesis of these biological materials.
How Bioreactors Operate
Bioreactors are available in various sizes and shapes, from tiny laboratory models to large industrial systems that may generate millions of vaccine doses. These reactors are especially important for the bacterial and viral vaccine production processes.
For Bacterial Vaccines
Bioreactors are used to cultivate the bacteria in a nutrient-rich environment to produce bacterial vaccines, such as those for diphtheria or tetanus. Because they can precisely manage the conditions that allow bacteria to multiply, fermenters are frequently the preferred bioreactor for bacterial growth. Bailun’s industrial fermenters, for instance, are made to encourage the best possible bacterial growth, guaranteeing large quantities of the bacteria required to produce vaccines.
For Viral Vaccines
However, a different configuration is needed for viral vaccines. Usually, the virus is grown in a host system, like animal cells, rather than directly. These cells, which are cultured in bioreactors, are where the viruses multiply. Fertilized chicken eggs have long been used as the growth medium for many viral vaccinations, including influenza. However, a more scaled and regulated approach to creating viral vaccines is provided by contemporary bioreactors, particularly those that use mammalian cell cultures.
Types of Bioreactors
A variety of bioreactor types are employed in the manufacturing of vaccines, each of which is appropriate for a particular vaccine type or production size.
Batch Bioreactors
The most basic and conventional kind of bioreactors are batch bioreactors, in which the entire process is completed in a single cycle. The reactor is cleaned, emptied, and ready for the subsequent batch after the product has been harvested. This technique is frequently applied to projects on a lesser scale.
Continuous Flow Bioreactors
Continuous flow bioreactors are utilized for larger, more effective production. They provide a steady flow of microorganisms or cells, increasing output and decreasing downtime in between batches.
Single-Use Bioreactors
The creation of disposable or single-use bioreactors is a recent advancement in bioreactor technology. These methods remove the requirement for thorough cleaning and sterilizing in between batches and lower the danger of contamination. This can drastically reduce expenses and speed up the production process.
Vaccine Bioreactors
Vaccine bioreactors are crucial instruments for producing vaccinations on a wide scale. They offer the ideal conditions for growing the cells, bacteria, or viruses utilized in vaccines, particularly in response to international needs such as COVID-19.
Challenges in Vaccine Manufacturing
Even with all of the advancements in vaccination technology, there are still difficulties in the process. Ensuring universal access to vaccines is one of the biggest obstacles. One significant obstacle is the cold chain, which we covered previously. This is particularly true in areas with limited resources, where it can be challenging to maintain reliable transportation and electricity.
Production capacity is another issue. Increased infrastructure, technology, and personnel training are necessary to meet the demand for vaccines worldwide, particularly during a pandemic. Here, bioreactor technology is essential. With their large-volume fermenters and bioreactors, companies such as Bailun Biotechnology offer scalable solutions that enable producers to produce vaccines in large quantities without sacrificing quality.
Obstacles may also arise from vaccine reluctance and public perception. Fear and false information might keep individuals from getting vaccinated, even when there are safe and effective vaccines available. In addition to technical answers, public health initiatives that raise awareness and foster vaccine trust are needed to address these issues.
What’s Up Next in the Production of Vaccines?
The manufacture of vaccines has a promising future. Automation, artificial intelligence, and synthetic biology developments have the potential to transform the sector completely. Researchers are developing “universal vaccines” that might offer widespread defense against various viral types, such as coronaviruses or the flu.
Decentralized production is also being promoted, which would allow smaller regional facilities to make vaccinations. This could simplify responding to future epidemics by easing the logistical burden of providing vaccines worldwide.
The time it takes to create and disseminate vaccinations may decrease even more as technology develops, bringing us one step closer to a time when we can react quickly to new diseases.
Conclusion
So, how does the manufacture of vaccines work? It’s a multi-step, intricate process that calls for advanced science, strict safety regulations, and international cooperation. Every stage, from the preliminary laboratory study to the large-scale manufacturing of bioreactors, is essential to guarantee the safety, efficacy, and accessibility of vaccines.
The next time you roll up your sleeves for a shot, remember that you’re getting more than just a small quantity of medication; you’re also reaping the benefits of decades of innovation, research, and innumerable hardworking experts.
Vaccines have revolutionized human health, and as the manufacturing process for vaccines advances, they will continue to be one of the most effective weapons in the fight against illness.
Are You All Set to Begin Producing Vaccines? If you want cutting-edge bioreactors, pick Bailun Technology!
Safety, effectiveness, and precision are non-negotiable in the manufacture of vaccines. You need the greatest equipment available to make sure your vaccine manufacturing process is efficient and up to the highest standards. Bailun Technology can help with that.
We provide a variety of cutting-edge bioreactors that are specially made to satisfy the requirements of contemporary vaccine manufacturing. Our bioreactors are designed to maximize growth conditions, preserve sterility, and offer unmatched scalability for everything from bacterial and viral culture to large-scale industrial fermentation.
Contact us now to advance the development of innovative vaccines!